EMF Technology in the Automotive Industry
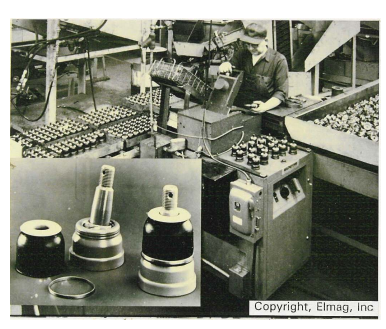
This 1965 picture shows the first magneform machine installed in industry by Elmag Staff at a General Motors Facility. The system assembles an automobile ball joint on which the neoprene boot is tightly secured to the housing with a copper ring. The ring is shrunk onto the boot with an electromagnetic pressure pulse, thus shrinking the ring and providing a 360 degree tight seal.
This 1965 picture shows the second magneform machine installed in industry by Elmag Staff at a General Motors Facility to secure neoprene boots onto the automobile constant velocity joints. When subjected to freezing temperatures, these joints are exposed to extreme stresses. The 360 degree tight seal avoids failure.
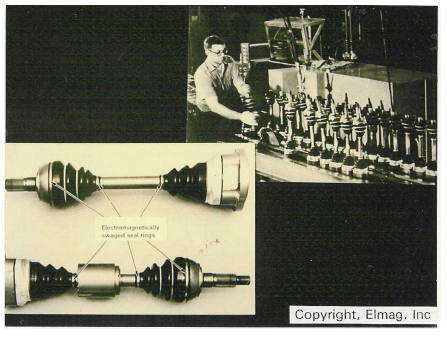
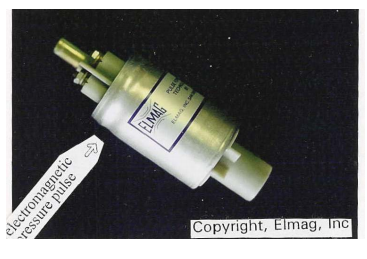
Electric Fuel Pump Assembly
Electromagnetic pressure pulses collapse the aluminum housing over the plastic end pieces.
Shock Absorber Components
A neoprene boot is secured 360 degree with a electromagnetic pressure pulse.
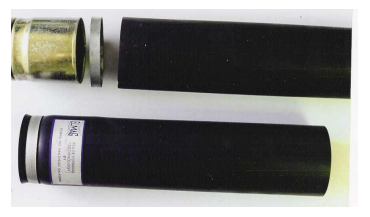
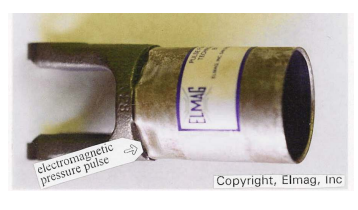
Steering Linkage Assembly
The steel tube is swaged with an electromagnetic pressure pulse onto a cast iron yoke. The actual tube is longer. This sample is a cut-off.
Automotive Drive Shaft Components
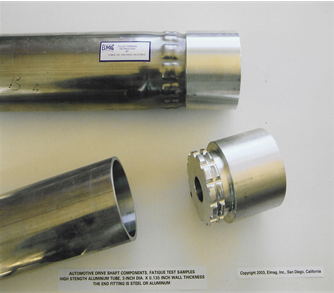
Test samples for automotive drive shaft. The material is 3mm wall thickness, high strength aluminum. Below is a picture of the MagnepulsTM machine used for the assembly of the drive shafts.
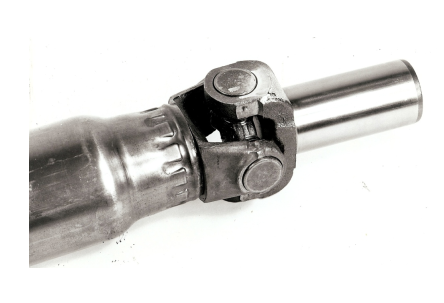
Finished drive shaft assembly. The tube material is 0.120 inch steel. The yoke is cast iron.
Elmag Sixty-kJ MagnepulsTM Machine with High Energy Electromagnetic Compression Coil to assemble the drive shaft components.
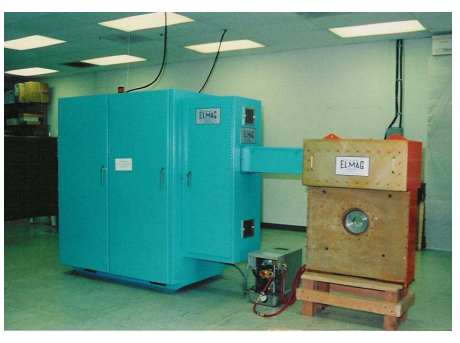